If you look up at the sky on a clear evening, the chances are that you will see a satellite silently drifting across the sky. As a 10 year old child, I remember sitting out at night with my father and feeling lucky to catch a glimpse of a satellite. These were rare events with only 400 active satellites in orbit at that time, today however, there are over 7,000 active satellites.
The exponential increase in numbers was kickstarted by the new space revolution launching mega-constellations designed to deliver broadband internet and telecommunication services anywhere on the planet. These satellites initially focused on radio frequency transmission for ground-to-satellite and satellite-to-satellite communication but there is a shift to the optical domain, bringing the benefits of lower latency, higher bandwidth, improved security and more efficient power conversion.
To achieve this, fiber optic amplifiers are used in a similar way to EDFAs in telecoms networks today, boosting the attenuated signal from one node to another. The key difference is that the space amplifiers require far higher signal power levels, not to overcome transmission attenuation (as they are transmitting through empty space), but to overcome the resultant beam divergence from transmitting in free space over hundreds of kilometres.
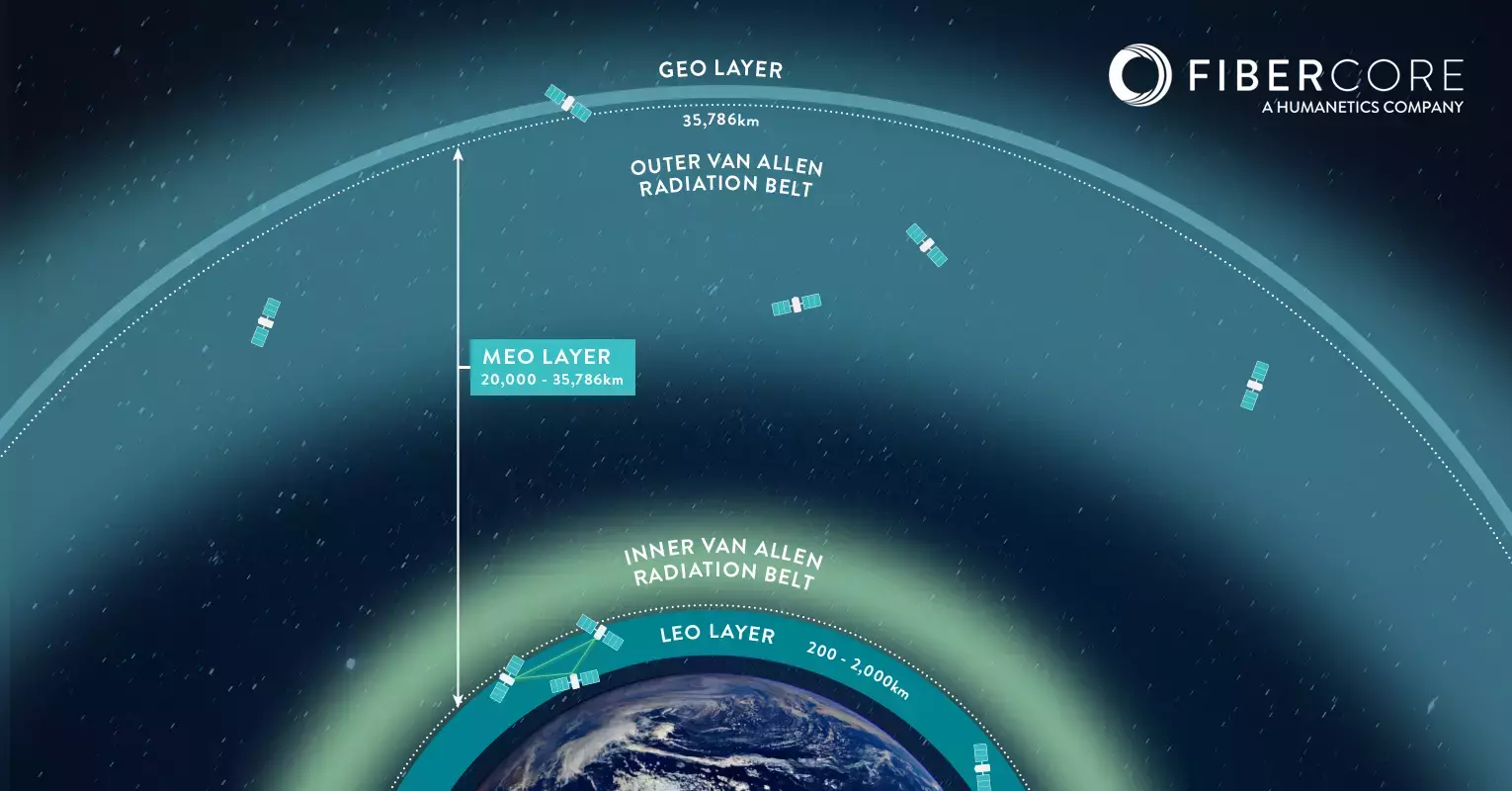
Figure 1: LEO, MEO and GEO orbits and their overlap with the Van Allen belts.
This results in large beam diameters of 10’s to 100’s of meters and, subsequently, very low coupling efficiency at the receiving satellite’s aperture. High power fiber amplifiers are subsequently used containing cladding pumped optical fiber with erbium-ytterbium doped cores in a double or, ideally for reliability, triple cladding design.
Beyond the power level, the requirement to survive in the vacuum of space is essential. For the glass this is a trivial matter but for the coatings, careful selection of the right materials is required to ensure outgassing and physical changes to the coating’s optical and mechanical properties do not occur. Cosmic radiation also presents an interesting challenge, but the scale of the challenge depends on the region of space the satellite is operating in and how the fiber is being used. Fibers have a trick up their sleeve to fight radiation, radiation induced damage can be partially or fully recovered through simply operating the optical fiber in a process known as photo-annealing.
For low earth orbit (LEO) satellites, which form the majority of existing and planned future satellites, the inner and outer Van Allen belts provide significant protection from cosmic radiation, see Figure 1. When coupled with the inherent radiation shielding provided by a satellite’s mechanical structure and photo-annealing, this can result in negligible radiation impact on the optical fibers. For higher altitude orbits, such as medium earth orbit (MEO) and geostationary earth orbit (GEO) the radiation levels become more extreme requiring optimized radiation insensitive optical fiber designs.
Over the last few years, Fibercore’s TC1500Y(11/125)HD ErYb high reliability triple clad fiber has been, and continues to be, actively deployed into LEO satellites.
I hope that I will soon be able to sit outside on a clear night with my sons and be able to point at a satellite going by and tell them that, in some little way, my colleagues and I helped get optical fiber onto that satellite.
Subscribe for Insights!
Register to receive Fibercore's latest key updates, events and relevant industry news
straight to your inbox!
Speak to our experts
Provide us with your information and our service team will contact you
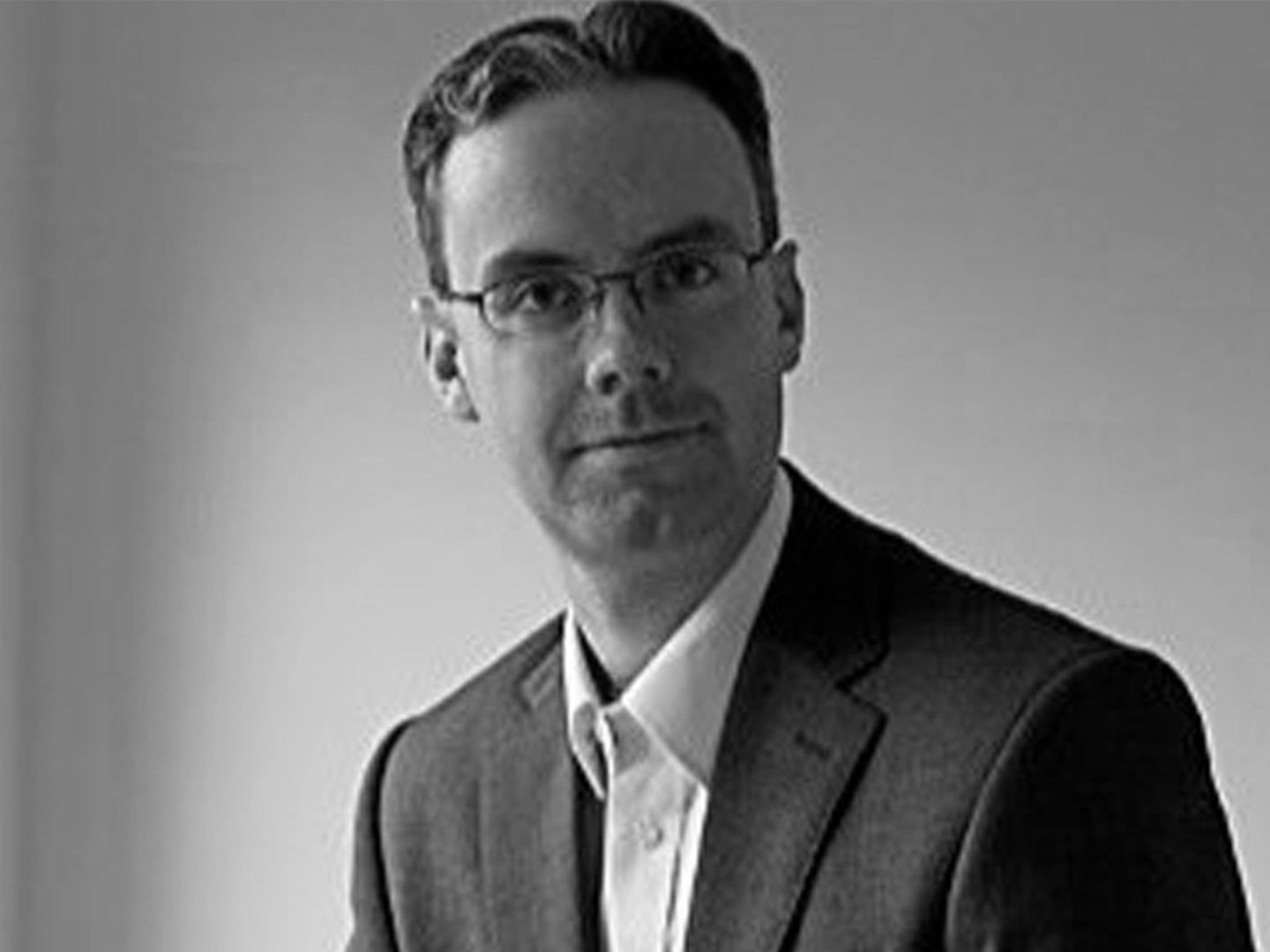
Dr. Andy Gillooly
Andy Gillooly the business development manager at Fibercore (Southampton, U.K.). In 2001, Andy graduated from the University of Birmingham, with a masters degree in physics and received a PhD in fiber Bragg gratings (FBGs) from Aston University, England. He spent over four years as a senior development engineer at SPI Lasers, developing FBGs and pulsed fiber lasers. After SPI, Andy joined Sharp Laboratories of Europe, responsible for the optical design and technical customer interactions for Sharp's wafer level camera project. Later, Andy joined Fibercore where he is currently responsible for driving the company forward into new markets with new products, he has currently been with Fibercore for 14 years.