Haptic Feedback for Laparoscopy
Haptic feedback is the ability to give touch sensation feedback from a remote device, such as a surgical tool at the end of a rod which gives an element of feedback to the surgeon.
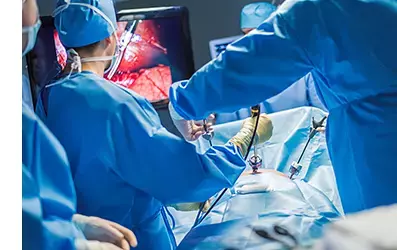
A laparoscopic surgical procedure (Fig. 1) also known as a minimally invasive surgery technique or keyhole surgery, is a way of conducting a major surgical procedure, but instead of having an open wound, for example slicing through abdominal muscles, the surgical team enter the body through 3 or 4 small portholes around the abdomen. This allows the patient to have a significantly shorter recovery time due to a lower level of trauma experienced by the body.
In the image above, the surgeon on the right is using 2 surgical tools which are located on the end of rods. Those surgical tools have to go through a pivot point at the entrance ports to pass through to the body. Due to that pivot point, all of the surgeon’s controls are reversed, so when the surgeon pushes the tool up, the screen shows the tool going down. When the surgeon pushes left, the tool tip goes right. So the surgeon has to reverse all of their motions in order to run this process, a tricky task! What makes it even more of a challenge is that the tools have to stick up a certain distance above the body which is not an ergonomic way of operating for a long procedure. Having your arms up with your body slightly bent over a patient is a difficult environment to work in and what makes this procedure even more tricky is having to run the procedure through a remote endoscopic view. So the surgeon isn’t seeing a direct image, it’s an indirect image with an indirect contact, through a reversed control mechanism. Laparoscopy is an extremely challenging process.
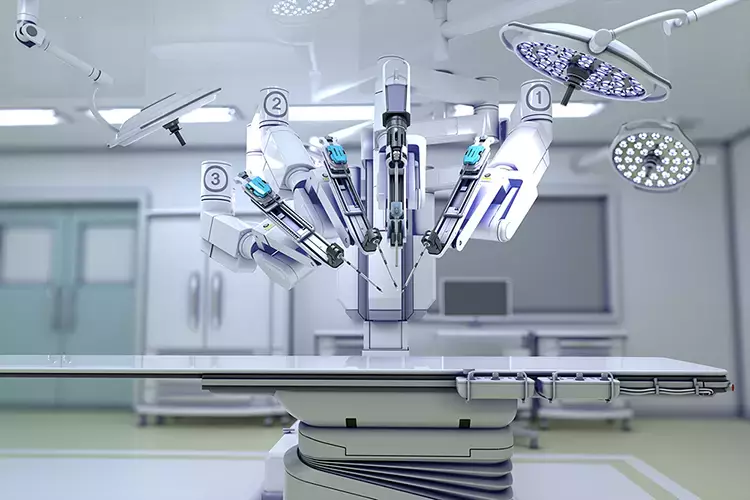
Figure 2: Sophisticated surgical robot.
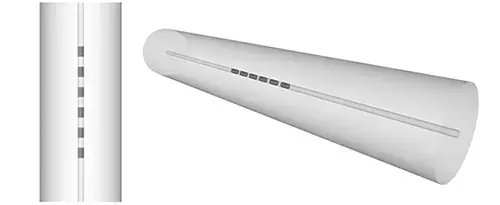
The development of sophisticated surgical robots allows the surgeon to be in a remote location, maybe in the same room, the room next door or even the other side of the world. The benefits are that the surgeon can have a much more comfortable experience of running that laparoscopic process and they don’t have to contend with inverting all of their movements. It could be argued that despite this advancement in technology, robots don’t have the ability to "feel", thus limiting the usability of surgical robots. This is no longer the case.
With the use of optical fiber, robot haptic feedback is now a reality. The surgeon can feel the resistance the robot is "feeling" during the procedure by incorporating a strain sensing Fiber Bragg Grating (FBG) into the tool. An FBG is a pattern that is written into the central core of an optical fiber (Fig 3) which can be customised to reflect a certain wavelength of light. If the optical fiber with the FBG is embedded in the tool then any strain, for example a longitudinal elongation, is represented as a linear shift up in the wavelength that this FBG reflects. Similarly if compression is present, the wavelength decreases. Therefore, you have a strain sensor that can be mounted onto critical parts of a surgical tool (Fig 4).
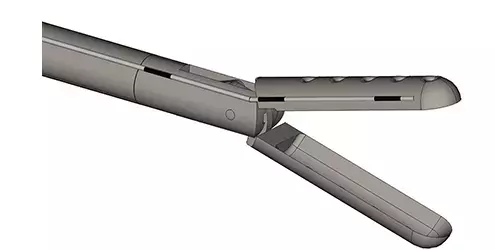
By mounting optical fiber with FBGs onto a surgical tool, you can start to see and analyse the exact strain that the tool is experiencing at various locations. Through considered placement of the FBGs, the surgeon would be enabled to feel the pinch force, thus removing barriers to the user interface being physically and sensory remote, bringing the sensor into the user experience.
Fibercore have the ability to provide these fibers assembled into sub-components or assemblies. This may include pre-stripped and cleaved ends or more complex stripped, cleaved, spliced, connectorized and mounted assemblies giving a plug-and-play type product. Please contact us for more information.
Fibercore have the ability to provide these fibers assembled into sub-components or assemblies. This may include pre-stripped and cleaved ends or more complex stripped, cleaved, spliced, connectorized and mounted assemblies giving a plug-and-play type product. Please contact us for more information.
Related Products
Customized arrays of FBGs can be created to enable multiple sensor points along a single optical fiber, giving just a single fiber/cable to manage. Electrical strain gauges require multiple wires per sensor point.
The SM1500 range of fiber give different numerical apertures (NA) which results in improved bend loss performance for tighter bend radii.